Magic Wrist
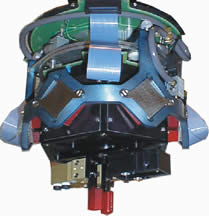
In this device, a body called the "flotor'' is magnetically levitated by the combined forces and torques from six Lorentz actuators, arranged at 60 degree intervals around a horizontal ring. Each actuator has a line of action at 45 degrees with respect to the vertical axis of symmetry. The permanent magnet structures of the actuators are attached to inner and outer stators which in turn are attached to the distal link of the robot arm coarse manipulator, whereas the coils of each actuator are contained in the thin, hexagonal flotor shell. The position and orientation of the flotor with respect to the stator is sensed by a triplet of optical beams projecting from the stator to a corresponding set of two-axis position-sensing photodiodes (PSDs) attached to the inside of the flotor. A set of three thin flexible ribbon cables provide power and signals to and from the flotor--the only mechanical connection between flotor and stator. The flotor has a motion range of plus or minus 5 mm in translation and plus or minus 4 degrees in rotation, a position resolution of approximately 1 micron, and a bandwidth of over 30 Hz.
Assembly workstations that perform many operations will often require various interchangeable tools and accommodation mechanisms. For the Magic Wrist, a variety of mechanisms, each of which may perform a special tool's motion, can be synthesized by changing the tool point position and the rotation matrices and gains of the controller by software. Furthermore, the synthesis of various mechanisms can be performed while the wrist is doing a given task. For example, a unidirectional slider, a single axis rotator, a two-dimensional slider mechanism, a ball and socket rotator and a programmable "remote center compliance" device can be synthesized about the point defined as the tool point. Once the mechanism is emulated, assembly can often proceed rapidly in a manner which is "open-loop" with respect to the task, i.e. without need for task parameter force-torque sensing or programmed decision making.